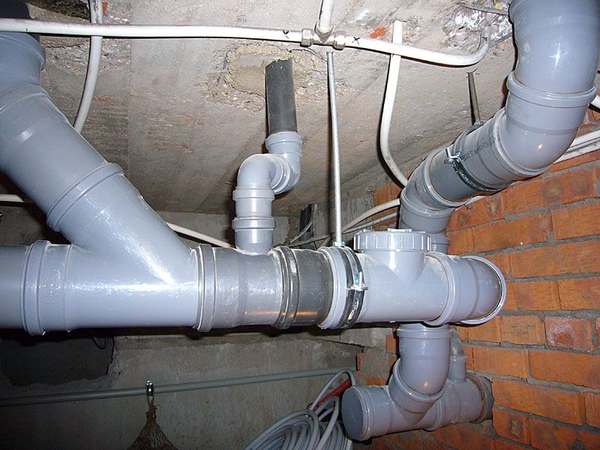
Именно в таком ключе проходит беседа Джеймса Снодграсса с валлийским лицензиатом технологий Weholite и WehoPanel о том, как полиэтилен высокой плотности заменяет бетон в канализационной инфраструктуре Великобритании и Норвегии.
Сейчас экструдированные трубы из полиэтилена высокой плотности всё чаще используются в инфраструктурных проектах в качестве замены традиционным материалам. Теперь даже канализационные сооружения, которые традиционно строились из сборного железобетона, стали создавать из экструдированного полимера.
Anglia Water– компания, обслуживающая Восточную Англию в Великобритании. В августе специалисты Anglia Water установили новую канализационную систему, камера её насосной станции изготовлена из полиэтилена высокой плотности, а не из привычного бетона.
Трубы – и насосная станция – для этого проекта были произведены в Уэльсе компанией Asset International. Эта компания является британским лицензиатом Weholite и WehoPanel Systems, развитием которой занимается финская KWH (сейчас она входит в совместное предприятие Uponor Infra).
Насосная станция для Кембриджских канализационных очистных сооружений составляет 15 метров в длину, 4,5 метра в ширину и 5 метров в высоту. Её доставили 12 августа в виде двух секций, которые были собраны и сварены уже на месте.
Саймон Томас, управляющий директор Asset International, объяснил технологию Weholite: «Труба изготавливается из полого профиля, который мы производим методом экструзии с использованием стандартного экструзионного оборудования. То есть, на самом деле, вместо трубы мы изготавливаем профиль с прямоугольным поперечным сечением. А уже потом, чтобы сделать эту трубу, мы наматываем его [прямоугольный профиль] вокруг барабана с нужным диаметром».
В процесс изготовления WehoPanel не входит этап намотки. Томас сказал: «В этом случае мы только нарезаем профиль на куски необходимой длины до того, как он будет направлен к барабану. Таким образом, мы получаем прямые отрезки профиля. У нас есть оборудование, которое позволяет сваривать их вместе, для того чтобы собирать панели WehoPanels».
«У нас есть команда обработчиков, которые придают WehoPanels самые странные и удивительные формы; в данном случае огромная панель должна была играть роль насосной станции. Элементы панели размером около 250 мм в ширину сваривали на оборудовании во фрагменты шириной 2 метра. Я сравниваю этот процесс с изготовлением гипсокартона. Сваренные на оборудовании профили превратились в панели шириной 2 метра. Окончательный вид такие панели обретают в нашем заводском цехе, там двухметровые фрагменты сваривают уже вручную».
Соединяются панели путём экструзионной сварки. Саймон объяснил: «Мы используем портативный аппарат на основе винта Архимеда, к верхней части которого прикреплён вентилятор горячего дутья; он нагнетает горячий воздух температурой около 200°С на присадочный пруток, который, расплавляясь, затем проходит через шнек. По сути, это мини-экструдер с выходом 5 кг в час».
Компания Asset приступила к производству труб в 1996 году, тогда были запущены две линии, позволяющие производить трубы до 2,2 метра в диаметре. В 2000 году была добавлена третья линия – для производства труб диаметром 3 метра.
«В 2008 году мы пошли дальше», – заметил Томас. – «И оборудовали четвертую линию, чтобы производить трубы диаметром до 3,5 метров, а это, как вы можете себе представить, чертовски большие трубы».
«В отличие от цельных нагнетательных труб, здесь вы имеете дело с лёгким материалом. Следовательно, метр трубы диаметром 3,5 метра весит всего 500 кг. Но когда эта труба установлена, её качества позволяют ей выдерживать нагрузку на дорожное полотно в полной мере».
Компания начала делать WehoPanels только в 2013 году. Томас сказал: «Мы вложили средства в оборудование для изготовления WehoPanel и в сентябре прошлого года ввели его эксплуатацию. На сегодняшний день она [насосная станция] является крупнейшей в мире системой, сделанной из нашей продукции».
«Интересно, что изначально она должна была быть сделана из сборного железобетона. Мы доставим её двумя секциями – но лишь по причине ограничений по высоте, накладываемых транспортом. Она будет закреплена на бетонном основании, а затем – после небольших работ по сварке на месте, необходимых для того, чтобы запечатать места стыков – она будет готова к эксплуатации».
«Если бы она создавалась из бетона, доставить её можно было бы лишь по частям, которые собирались бы уже на месте, что заняло бы намного больше времени и потребовало бы привлечения большего числа людей, а также большего количества оборудования. В то время как сборка нашей системы занимает всего лишь несколько дней. Это приводит не только к экономии времени и денег, но и к сокращению выброса парниковых газов, что станет очень хорошей новостью для представителей отрасли водоснабжения».
В будущем Asset планирует создавать более крупные системы, и сейчас специалисты компании работают над проектом камер для комбинированной системы канализации и защиты от переполнения. «Он уникален для отрасли водоснабжения», – сказал Томас. – «Существует много комбинированных систем водоснабжения и канализации, которым необходимы камеры для фильтрации воды в случае шторма».
Пока что компания только разрабатывает проект. Будущую систему моделируют при помощи программы CAD 3D: создателям необходимо убедиться, что она надёжна, перед тем, как переходить к стадии производства.
Томас признаёт, что из-за давления трубы, как правило, не очень хорошо переносят транспортировку – особенно трубы такого большого диаметра. Но у Asset International имеются рынки экспорта. В августе, например, компания поставила трубы различного диаметра для использования в качестве дорожных водопропускных труб на территории Фолклендских (Мальвинских) островов – а это путешествие почти в 13 000 км.
«Также мы получили хороший заказ на изготовление дорожных водопропускных труб для Северной Норвегии», – поделился Томас. – «И это будут трубы диаметром 3,5 метра; просто мы единственные, кто делает это в Европе… или в мире. Но, наверное, мне не стоит так опрометчиво рассуждать. Раз в год мы получаем заказ от властей того или иного северного района Норвегии, потому что они предпочитают использовать трубы большого диаметра из пластмассы, а не из традиционных материалов – ведь они могут подвести в экстремальных погодных условиях, с которыми люди сталкиваются за полярным кругом».
Asset утверждает, что проектный срок службы труб составляет 120 лет – эти данные были получены в ходе тестирования с использованием экстраполяции и моделирования процесса старения, проведённого производителями материалов.